Perdue U. Part of National Effort to Reduce Fuel Consumption by 20%
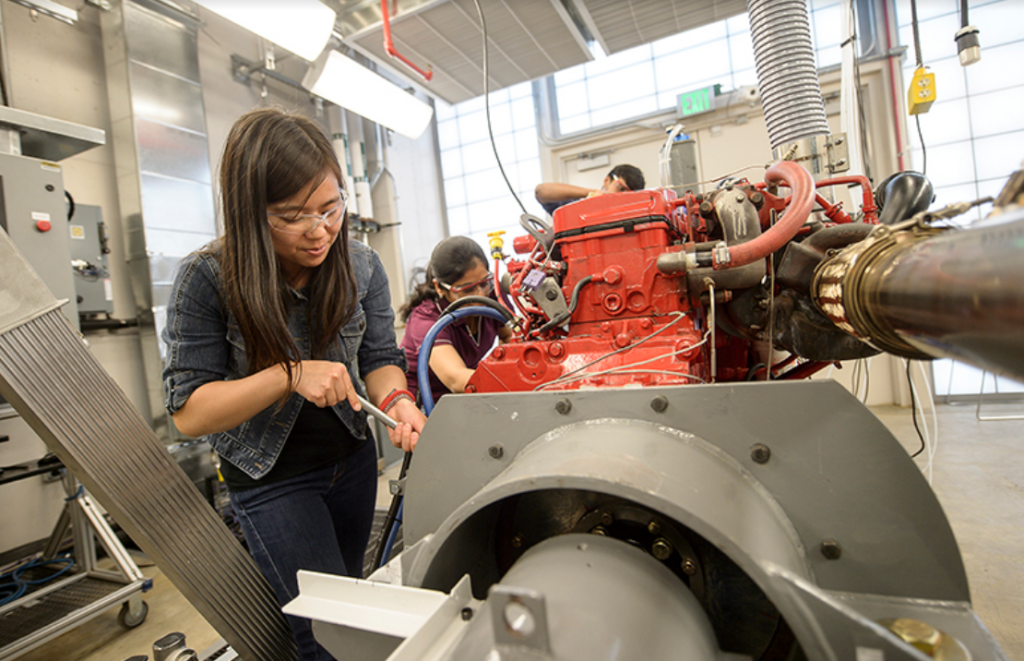
Former Purdue graduate students Sylvia Lu, left, and Mayura Halbe work in the Cummins Power Laboratory at Purdue’s Ray W. Herrick Laboratories. (Purdue University photo/Charles Jischke)
Purdue University is leading part of a national effort to reduce vehicle fuel consumption by 20 percent through automated systems that interconnect cars and trucks and the transportation infrastructure using sensors and online cloud technology.
The U.S. Department of Energy’s Advanced Research Projects Agency-Energy (ARPA-E) has announced up to $32 million in funding for 10 projects as part of its Next-Generation Energy Technologies for Connected and Autonomous On-Road Vehicles (NEXTCAR) program.
Purdue leads a project focusing on Class 8 trucks, namely tractor-trailers, and will work with team members Cummins Inc., Peloton Technology, Peterbilt Motors Co., the National Renewable Energy Laboratory and ZF TRW.
The need is real and its big. Here’s why: Because heavy-duty trucks consume a significant percentage of total fuel used in the United States, reducing the fuel consumed by those vehicles would have a significant impact on overall vehicle energy usage.
The Purdue-led team will receive $5 million over three years for its project, which begins in March.
“This project is specific to developing fuel-saving algorithms that depend on connectivity,” said Gregory Shaver, a Purdue professor of mechanical engineering who is leading the team. “Trucks will be connected to the cloud, and they will be connected to each other.”
Much of the research will be performed in Herrick’s Cummins Power Laboratory. Engineers from Cummins, a leading manufacturer of diesel engines, will spearhead the development of algorithms needed to operate the engine and related systems. The project also will involve four Purdue graduate students.
The Purdue team will pursue three concepts: on-the-fly recalibration of the engine and transmission to constantly adapt to new conditions; running model-based control algorithms from the cloud as the vehicle is driving; and platooning with enhanced capabilities, such as synchronizing transmission shifting between two trucks.
The vehicles will tap into forward-looking information that reveals changes in road, traffic and driving conditions several miles ahead. Each truck will be connected to a cloud-based network operations center, enabling access to information from crowd-sourced traffic data, road-grade maps and weather services.
New algorithms will allow “platooning” for trucks, which is much like positioning racecars close to each other to reduce aerodynamic drag.
Peloton Technology’s platooning system provides a wireless vehicle-to-vehicle (V2V) communications link between the throttle and braking systems of pairs of trucks, allowing the trucks to coordinate speeds and maintain a safe, aerodynamic following distance. Optimizing the powertrain via information about the road ahead allows for significant enhancements to platooning algorithms. Today, platooning with the Peloton Technology two-truck platooning system results in average fuel savings of 7 percent at a following distance of 36 feet, based on 4.5 percent fuel savings for the lead truck and 10 percent for the following truck. Enhanced algorithms promise to boost average fuel savings from platooning to as much as 13 percent.
The new technologies are being designed for both highway and cities, but the project’s emphasis is on highway operation.
The team will demonstrate the technology by the end of the three-year project.
One requirement is that the commercial cost of the added technology not exceed $3,000, underscoring the importance of creating a market pathway to improving the fuel and energy efficiency of heavy trucks.
Category: Commercial